
Why the Large-Scale Stamping Machine for Auto Parts Is a Game-Changer
In the modern automotive industry, precision and efficiency are key to staying competitive. The large-scale stamping machine for auto parts has become an essential tool for manufacturers aiming to boost output while maintaining top-quality standards. As vehicle designs grow more complex and production demands increase, this machine delivers consistent, high-speed performance without sacrificing accuracy.
At Guangduan, we recognize the importance of aligning advanced technology with real-world production needs. That’s why our STPP Series large-scale stamping machines are designed to meet these exact challenges – offering robust performance, enhanced reliability, and the flexibility required for modern automotive manufacturing.
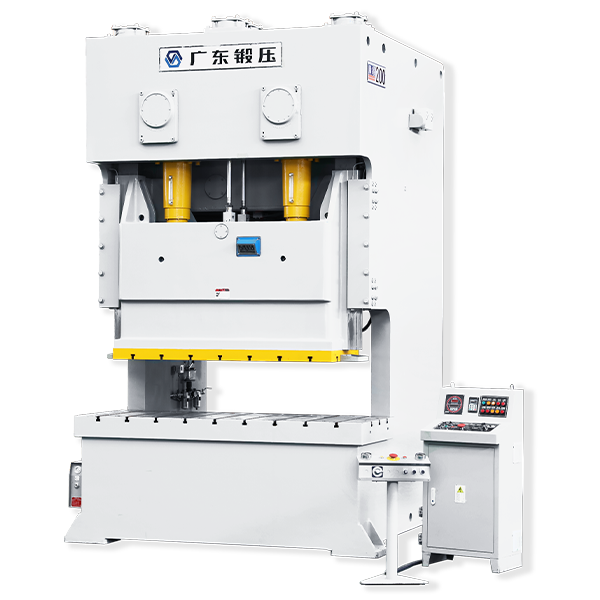
Revolutionizing Auto Parts Production
Auto manufacturers face constant pressure to reduce costs and shorten lead times. Traditional stamping methods can struggle with heavy-duty dies, large sheets, and high-volume demands. Enter the large-scale stamping machine for auto parts, designed specifically to handle these challenges. By offering greater force, stability, and speed, it transforms stamping operations from a bottleneck into a streamlined, high-output process.
Advantages of Large-scale Stamping Machine for Auto parts
The benefits of this game-changing equipment extend across multiple facets of production:
✅ Enhanced Rigidity – Our machine body is welded from thick steel plates, ensuring minimal vibration and consistent part dimensions.
✅ Balanced Motion – Dual crankshafts are reversed to counter side forces, reducing wear on linkages and extending maintenance intervals.
✅ Precise Guidance – Eight-sided full guide rails on the slider provide superior anti-unbalance capacity, low lateral force, and exceptional retention of accuracy.
✅ Rapid Overload Protection – A hydraulic overload device within the slide block reacts instantly to abnormal loads, protecting both tooling and press components.
✅ Durable Wet Clutch – A high-torque wet clutch delivers smooth engagement and long service life, operating quietly and cleanly.
✅ Intelligent Control – PLC integration allows for customizable stroke patterns, quick parameter adjustments, and seamless communication with other automation devices.
Technical Innovations Behind the STPP Series
The heart of our large-scale stamping machine for auto parts lies in its innovative design. Engineers at Guangduan leveraged decades of forging experience to optimize every component for maximum performance.
Robust Construction and Precision
The STPP Series’ frame is built from fully stress-relieved steel assemblies. This rigidity prevents frame deformation under heavy loads. The dual crankshaft design not only balances inertia forces but also reduces the pushing force on link blocks. Meanwhile, the eight-sided guide rails on the slider guarantee consistent part quality by limiting lateral play to mere microns. Such precision is vital when producing components like chassis brackets or engine mounts, where tolerances are tight and part reliability is non-negotiable.
Advanced Safety and Control Systems
Safety and control go hand in hand. Our machines integrate:
• Hydraulic Overload Protection – Sensors detect force spikes and halt operation before damage occurs.
• Emergency Stop Mechanisms – Strategically placed e-stop buttons and safety interlocks ensure immediate shutdown in hazardous scenarios.
• PLC-Centric Automation – From single-machine setups to fully automated stamping lines, our PLC modules manage sequences, monitor performance, and log key metrics for continuous improvement.
• Human-Machine Interface (HMI) – A user-friendly touchscreen offers intuitive navigation, recipe saving, and real-time diagnostics.
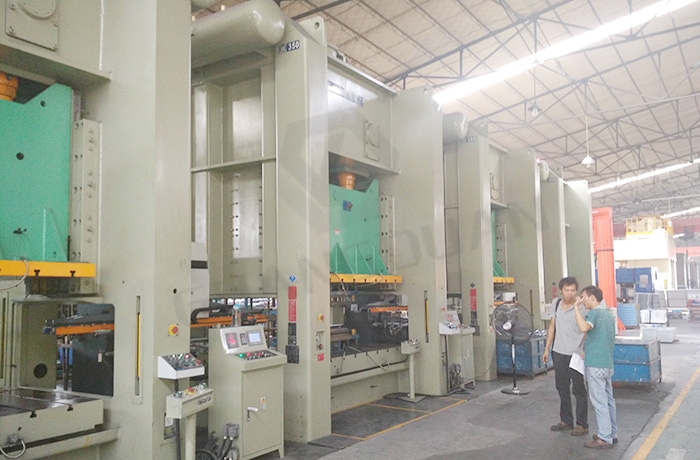
Realizing Automation and Efficiency
Automation is no longer a luxury – it’s a necessity. The large-scale stamping machine for auto parts excels in interfacing with uncoilers, feeders, transfer systems, and robotic loaders. By linking multiple presses into a unified production cell, manufacturers can achieve:
• Higher Throughput – Continuous material supply and synchronized operation minimize downtime.
• Quality Consistency – Automated checks and feedback loops maintain uniform part dimensions across millions of cycles.
• Labor Optimization – Skilled operators can oversee several machines at once, focusing on process improvement rather than manual loading.
Seamless Integration with Production Lines
At Guangduan, we provide turnkey solutions. Our team assesses your current workflow, specifies the ideal STPP configuration, and engineers custom integration points. Whether you need a standalone press or a complete stamping line, our expertise ensures rapid deployment and minimal disruption.
Our Commitment to Research and Development
We’re not just equipment suppliers – we’re innovators. At Guangduan, we’ve established:
✅ Postdoctoral Research Station
✅ Guangdong Forging Equipment Engineering Technology R&D Center
✅ Guangdong Provincial Enterprise Technology Center
✅ Guangdong Key Laboratory of Metal Forming Processing and Forging Equipment Technology
Through these institutes, we’ve undertaken nearly 60 national, provincial, municipal, and district-level science and technology projects. This robust R&D ecosystem fuels continuous enhancements to our large-scale stamping machine for auto parts. We collaborate with universities and industry partners to explore new materials, adaptive control algorithms, and predictive maintenance strategies.
Embracing the Future of Auto Parts Manufacturing
The automotive sector is on the brink of transformative change. Electric vehicles, lightweight materials, and modular designs demand stamping solutions that can adapt quickly and perform reliably. Our large-scale stamping machine for auto parts meets these evolving needs head-on:
• Flexible Tooling – Quick-change die systems allow rapid switchovers between models.
• Eco-Friendly Operation – Energy-efficient hydraulics and regenerative braking lower power consumption and carbon footprint.
• Data-Driven Insights – Integrated sensors feed production data into cloud platforms, enabling real-time analytics and proactive maintenance.
As manufacturers worldwide pivot to smarter, greener production, the role of large-scale stamping machines becomes even more critical. By investing in scalable, precise, and automated stamping technology, companies can secure a competitive edge, reduce waste, and accelerate time to market.
Final Thoughts
The automotive industry is evolving fast – with electric vehicles, intelligent manufacturing, and rising global standards reshaping every corner of production. At Guangduan, we’re here to help you stay ahead with our cutting-edge large-scale stamping machines for auto parts.
Whether you’re scaling operations, replacing aging equipment, or starting a brand-new facility, our machines deliver the performance, precision, and durability your production demands. Let’s shape the future of auto manufacturing – one high-quality stamped part at a time. Contact us today to explore the next step forward.
CONTACT US

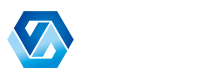
Guangdong Metal Forming Machine Works Co., Ltd.
We are always providing our customers with reliable products and considerate services.
If you would like to keep touch with us directly, please go to contact us