
How Do Hydraulic Presses 2024 Achieve Energy Efficiency?
Uncover the latest innovations in Hydraulic Presses 2024 technology. Delve into groundbreaking safety enhancements, global regulatory compliance, and proactive maintenance strategies. Discover the fusion of automation and robotics, alongside the progression towards eco-conscious designs. Stay abreast of emerging trends from industry leaders such as GUANG DUAN, guaranteeing enhanced performance, safety, and environmental sustainability across industrial sectors.
Introduction to Energy Efficiency in Hydraulic Presses
1.1 Importance of Energy Efficiency
Energy efficiency is a critical consideration in industrial machinery, including hydraulic presses. In 2024, manufacturers like GUANG DUAN are prioritizing energy-efficient designs to reduce operating costs, minimize environmental impact, and comply with regulatory requirements. Hydraulic presses play a vital role in various manufacturing processes, and optimizing their energy efficiency can lead to significant savings and sustainability benefits.
1.2 Key Factors in Achieving Energy Efficiency
Achieving energy efficiency in hydraulic presses involves various factors, including innovative technologies, design optimizations, and operational practices. By addressing these key factors, manufacturers can enhance the performance and sustainability of hydraulic press systems while minimizing energy consumption.
Technologies for Energy Efficiency
2.1 Variable Displacement Pumps
Variable displacement pumps are a cornerstone of energy-efficient hydraulic press design. These pumps adjust their output to match the required load, delivering hydraulic fluid at the precise pressure and flow rate needed for each operation. By avoiding energy wastage associated with constant-speed pumps, variable displacement pumps significantly reduce energy consumption and improve overall efficiency.
2.2 Servo Motors
Servo motors offer precise control over the movement of hydraulic press components, such as the ram and hydraulic cylinder. By adjusting speed, torque, and position in real time, servo motors optimize energy usage and minimize losses. Their high efficiency and responsiveness make them ideal for applications where precise control is essential, contributing to overall energy efficiency in hydraulic press operations.
2.3 Energy Recovery Systems
Energy recovery systems capture and reuse the kinetic energy generated during the press’s operation, converting it back into electrical energy. By harnessing this otherwise wasted energy, these systems help to reduce overall energy consumption and increase efficiency. Energy recovery systems are particularly effective in applications with frequent start-stop cycles, where significant energy savings can be achieved.
Design Optimization for Energy Efficiency
3.1 Efficient Hydraulic Circuit Design
Efficient hydraulic circuit design is essential for maximizing energy efficiency in Best Hydraulic Presses 2024. By optimizing the layout of hydraulic components, minimizing pressure drops, and reducing fluid leakage, manufacturers can minimize energy losses within the hydraulic system. Advanced design techniques, such as the use of flow control valves and proportional valves, help to ensure smooth and efficient operation while conserving energy.
3.2 Heat Management
Effective heat management is critical for maintaining energy efficiency in hydraulic presses. Excessive heat buildup can lead to energy losses and reduce the efficiency of hydraulic components. Manufacturers employ various heat management strategies, such as cooling systems, heat exchangers, and thermal insulation, to dissipate heat and maintain optimal operating temperatures. By preventing overheating and minimizing energy losses, these systems contribute to overall energy efficiency.
3.3 Lightweight and High-Strength Materials
The use of lightweight and high-strength materials in hydraulic press construction can improve energy efficiency by reducing the mass of moving components. Lighter components require less energy to accelerate and decelerate, resulting in lower energy consumption and improved overall efficiency. Additionally, high-strength materials enhance structural integrity, allowing for the design of more compact and efficient hydraulic presses.
Operational Practices for Energy Efficiency
4.1 Optimal Operating Parameters
Optimizing operating parameters, such as pressure, speed, and cycle times, is essential for maximizing energy efficiency in hydraulic press operations. By selecting the most suitable parameters for each application and ensuring proper synchronization of press components, manufacturers can minimize energy consumption while maintaining high levels of productivity and performance.
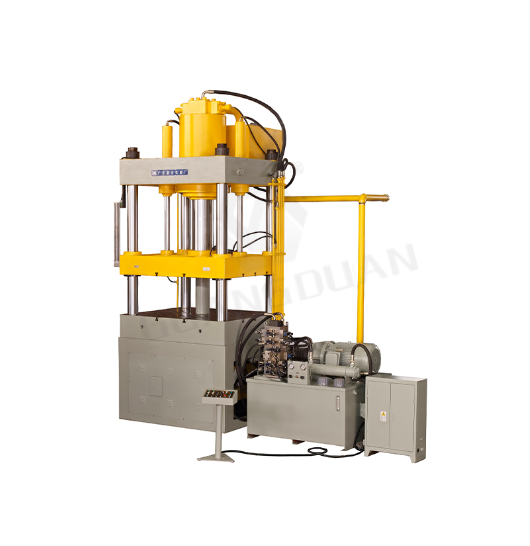
4.2 Regular Maintenance and Inspection
Regular maintenance and inspection are crucial for preserving energy efficiency in hydraulic presses. Routine tasks, such as checking hydraulic fluid levels, inspecting seals and hoses for leaks, and lubricating moving parts, help to ensure smooth operation and prevent energy losses due to component wear or malfunction. By identifying and addressing potential issues early on, manufacturers can maintain optimal energy efficiency and prolong the lifespan of hydraulic press systems.
4.3 Operator Training and Awareness
Operator training and awareness play a vital role in maximizing energy efficiency in Hydraulic Presses 2024 Best operations. Well-trained operators understand the importance of energy conservation and are proficient in operating the press at optimal efficiency levels. By promoting a culture of energy awareness and providing ongoing training and support, manufacturers can empower operators to make informed decisions that contribute to overall energy efficiency.
Applications of High-Quality Hydraulic Presses 2024
5.1 Stamping
Hydraulic Presses 2024 are widely used in stamping processes, where sheets of metal are formed into specific shapes. The consistent and precise force applied by hydraulic presses ensures high-quality results with minimal defects. Stamping is commonly used in the automotive and aerospace industries to produce complex metal parts.
5.2 Bending
Bending is another critical application of hydraulic presses in metal forming. The press applies force to a metal sheet, causing it to bend at a specified angle. This process is essential for creating components like brackets, enclosures, and structural elements. Hydraulic presses offer the control and accuracy needed for precise bending operations.
5.3 Deep Drawing
Deep drawing involves pulling a sheet of metal into a die to create a hollow shape. Hydraulic presses are ideal for this process due to their ability to maintain consistent pressure and speed. This ensures that the metal flows smoothly into the die, resulting in high-quality, uniform parts. Deep drawing is commonly used in the production of containers, sinks, and automotive components.
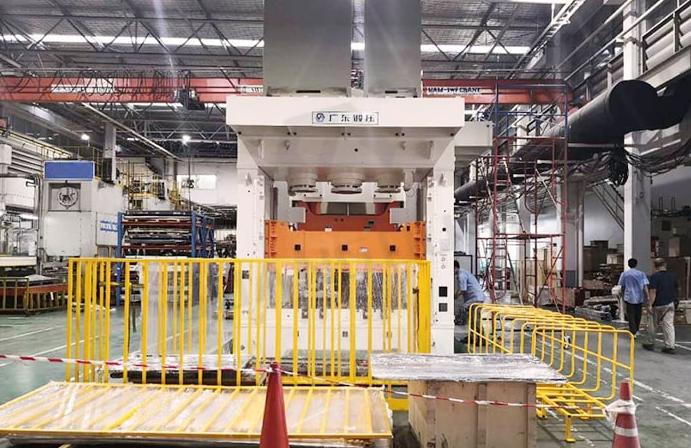
Safety Features and Regulations
6.1 Modern Safety Features
In the realm of industrial machinery, safety is of paramount importance, especially in the operation of hydraulic presses. Hydraulic Presses 2024 manufacturers like GUANG DUAN have prioritized the integration of advanced safety features into their hydraulic press designs. These features include technologies such as light curtains, safety mats, and emergency stop buttons. Light curtains create an invisible barrier around the press, and if this barrier is breached by any object or individual, the press immediately halts its operation. Similarly, safety mats placed strategically around the press detect pressure and trigger an emergency stop if someone steps on them. These features work in unison to prevent accidents and ensure the safety of operators and workers in the vicinity of hydraulic presses.
6.2 Compliance with Standards
Hydraulic press manufacturers must adhere to stringent international safety standards and regulations to ensure the safety of their equipment. Standards such as ISO 13849 and regulations set forth by organizations like the Occupational Safety and Health Administration (OSHA) outline specific safety requirements that hydraulic presses must meet. Regular inspections and audits are conducted to verify compliance with these standards. Adherence to these regulations not only promotes a safe working environment but also minimizes the risk of workplace injuries and accidents. Manufacturers like GUANG DUAN prioritize compliance with safety standards to ensure the reliability and safety of their hydraulic press systems.
Future Trends
6.1 Automation and Robotics
Automation and robotics are shaping the future of hydraulic press technology, revolutionizing manufacturing processes and increasing efficiency. In 2024, manufacturers are integrating robotics with hydraulic presses to automate material handling tasks. Automated systems can handle the loading and unloading of materials, reducing manual labor and increasing production speed and consistency. Robotics also enable precise positioning of materials, resulting in higher quality finished products. By embracing automation, manufacturers like GUANG DUAN are optimizing production processes and staying competitive in the global market.
7.2 Eco-Friendly Designs
Environmental sustainability is a driving force behind future hydraulic press designs. Manufacturers are increasingly focused on developing eco-friendly solutions that minimize environmental impact. One key aspect is the use of biodegradable hydraulic fluids, which reduce the risk of environmental contamination in the event of a leak or spill. Additionally, materials used in hydraulic press construction are being chosen for their eco-friendliness, with an emphasis on recyclability and sustainability. Energy-efficient designs are also gaining traction, with efforts to reduce energy consumption and lower carbon emissions. By embracing eco-friendly designs, manufacturers are not only reducing their environmental footprint but also contributing to a more sustainable future for the manufacturing industry.
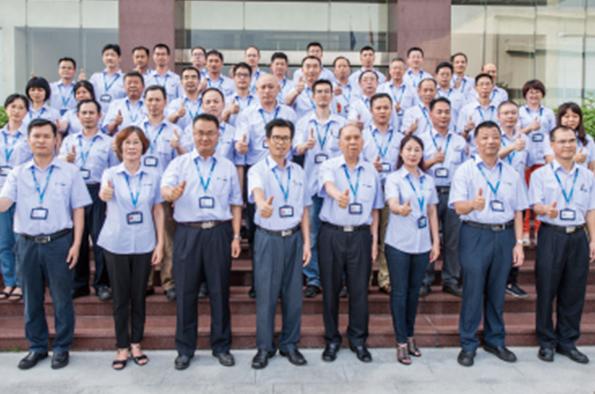
Conclusion
The Hydraulic Presses 2024 remains a cornerstone of modern manufacturing, continuously evolving to meet the demands of various industries. In 2024, technological advancements such as IoT integration, AI-driven predictive maintenance, and energy-efficient designs are enhancing the capabilities and efficiency of hydraulic presses. Their applications span from metal forming and composite material manufacturing to recycling, demonstrating their versatility and indispensability. As manufacturers like GUANG DUAN continue to innovate, hydraulic presses will undoubtedly play a pivotal role in shaping the future of manufacturing.
CONTACT US

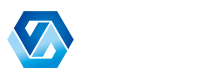
Guangdong Metal Forming Machine Works Co., Ltd.
We are always providing our customers with reliable products and considerate services.
If you would like to keep touch with us directly, please go to contact us